An ambitious research project funded with about 600.000 EUR by the German Ministry for Education and Research started in 2016 in cooperation with the University of Applied Sciences Würzburg-Schweinfurt (FHWS), the EiiF and the following partners: VIB (Dutch insulation contractors’ association), KAEFER Isoliertechnik GmbH & Co.KG, Hertel BV, Bilfinger OKI Isoliertechnik GmbH, G+H Isolierung GmbH, Knauf Insulation, Arnold Group and GWK Kuhlmann GmbH.
The goal: the combination of infrared technology with 3D scanning for TIPCHECK and energy efficient insulation purposes.
TIPCHECKs (Technical Insulation Performance Checks) deliver already today figures and payback estimates of potential energy savings of industrial production processes which are -or should be- insulated. The potential is large and the payback times with an average of 1-2 years are economically very convincing, as shown in the EiiF’s first TIPCHECK Report evaluating 180 energy audits in the same number of plants in Europe and beyond.
Today TIPCHECK engineers are using thermography to inspect already insulated systems for hot or cold spots causing costly energy losses for asset owners and even more severe problems like hazardous hot surfaces or corrosion under insulation (CUI) threats. Besides the inspections of the already insulated parts, thermography is also used to illustrate the significant and costly thermal losses of typically uninsulated special parts such as valves, pairs of flanges, etc.
The innovative idea of the so called eDIan (effiziente Dämmung von Industrieanlagen) university research project has the objective to develop a procedure which combines in one single operation the geometric data capture of the situation in a 3D STL or CAD file showing the situation “as built” with a thermographic data capture analysing the surface temperatures and resulting heat losses on the inspected plant equipment or complete installation.
The geometrical recording of the plant can be carried out by means of laser scanning, either with a base station with a geometrically known position and/or a mobile hand-held scanning device which scans the surfaces without touching them. By combining the 3D scanner with a thermographic camera, the infrared measured surface temperatures can be attributed to 3D measured surface dimensions and, like this, complete the TIPCHECK audit in one go.
Furthermore, with this collected information, the actual heat losses can be calculated, and the sizes and dimensions of special shapes like valves available as STL or CAD files can be further processed to build the tailored insulation solutions to stop the energy waste and repair the existing system. One of the biggest challenges of the research project is to find how to embed this information automatically into existing planning software to build the specific solution like tailored insulation boxes on valves or pairs of flanges.
The research as such is led by Prof. Dr. Eng. Stefan Knoblach from the FHWS’s laboratory for engineering and industrial surveying and Prof. Dr. Eng. Winfried Wilke from the FHWS’s laboratory for technical metrology and experimental stress. Together with their dedicated team, including scientific worker Sabine Roman and the project coordinator Sebastian Fiedler, and with the support of the two Master students Georg Karl and Philipp Grümpel the first steps have already been made.
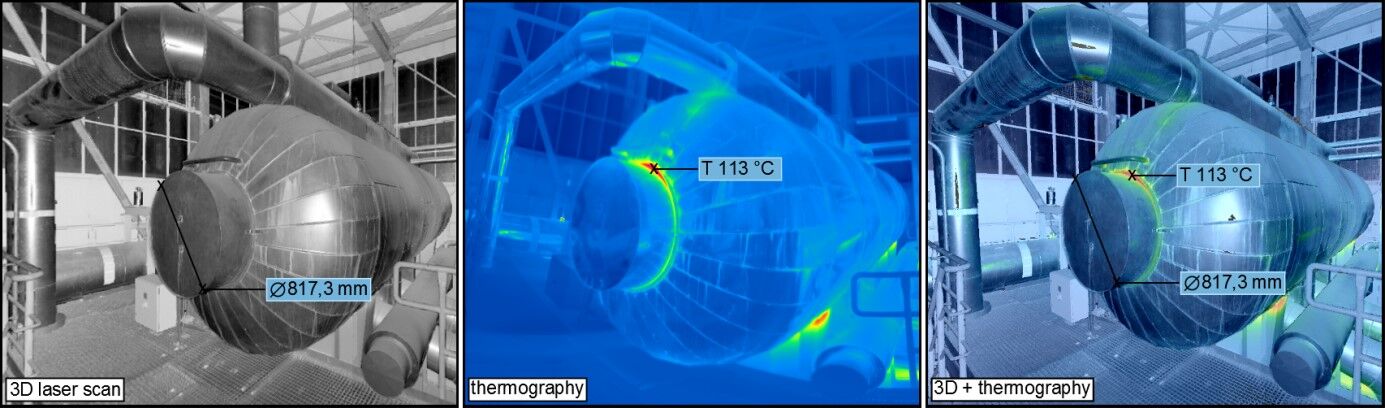
Left picture: Terrestrial 3D laser scan to digitalize the geometry. Middle picture: Thermographic image of the same object, hot areas are shown in red. Right image: Combination of 3D laser scan and thermographic image. Dimensions and temperatures of the object can be extracted from the measurement.
In its last meeting in 2016, the research project established a Steering Committee comprised by one representative of each partner and chaired by the EiiF Foundation Director Andreas Gürtler. The insulation experts (see picture below) and the University project team meet in regular workshops to give practical input, exchange experience and know-how and support that developments are very much focused on the TIPCHECK and insulation needs.
In this week’s workshop at the FHWS in Schweinfurt, on 15 and 16 February, the eDIan partners met and witnessed the first achievements, and further developed single working packages defining the next short to medium term goals:
-
Establish 3D semi-automatic elements from scanned uninsulated objects in an inexpensive and time efficient manner;
-
Develop a methodology to make quantitative temperature measurements on several hotspots in an existing installation.
After the workshop, the group of partners agreed that the research project is well on track but remains very challenging. We will further report about the progress of eDIan on the EiiF’s website and in our newsletter. Meanwhile, if you are interested to follow the developments of eDIan on a regular basis, please send an email to tipcheck@eiif.org with the subject “eDIan” and you will automatically receive regular updates on the project progress.
Back row from left to right: Jochen Falgner (FHWS), Marcel Kosch (FHWS), Andreas Gürtler (EiiF), Dr. Andreas Nuber (Wölfel), Prof. Stefan Knoblach (FHWS), Fred Kuhlmann (GWK) and Jan Zanen (VIB). Front row from left to right: Dr. Andreas Günell (Wölfel), Dr. Markus Scholz (Wölfel), Sebastian Fiedler (FHWS), Philipp Grümpel (FHWS), Georg Karl (FHWS), Peter Stulen (Hertel), Sabina Roman (FHWS), Prof. Winfried Wilke (FHWS), Thomas Ortlieb (G+H), Gyna Galvis (KAEFER) and Frank Jüngerhans (KAEFER)